Have any concerns about the conformity and scannability of a barcode or a logistics label? Or have you received a complaint about this from a distributor? Members of GS1 Belgium & Luxembourg can have their barcodes verified free of charge by our customer support team, which has a number of verification devices for this purpose. Our team will then prepare a full verification report with recommendations for correction.
Please note: Verification takes on average 2 weeks. For urgent requests you can contact us by phone at + 32 2 229 18 80.
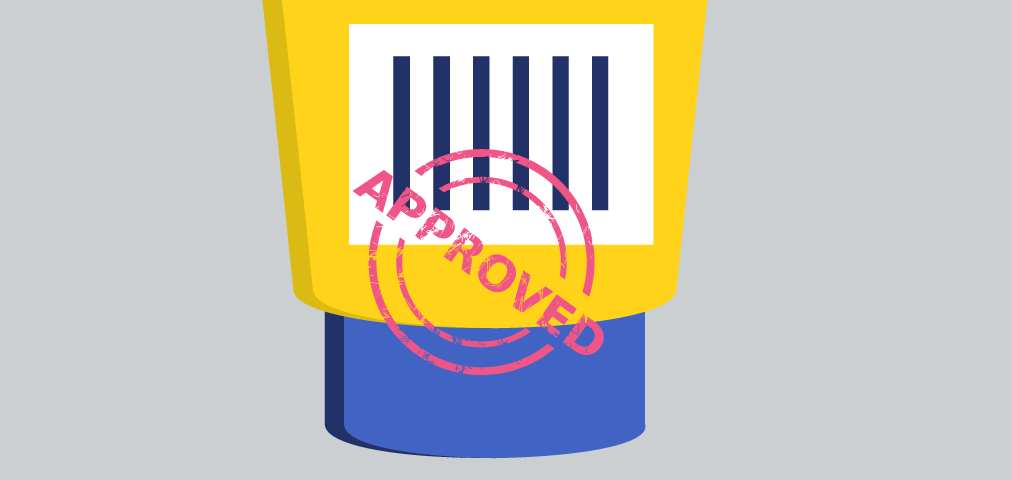
What can you send us?
- Barcodes on consumer packaging and outer packaging (of the types EAN/UPC, ITF-14, GS1-128, GS1 DataBar and GS1 DataMatrix)
- Logistics labels (pallet labels)
- Coupons
What should you keep in mind when sending your barcodes?
- For a correct assessment, we ask that you provide us with the original printed matter (no fax, no photocopy, no electronic file). In case of transparent packaging, it is a good idea to send us the packaging including the product content.
- In the application, always state the what language you would like the report to be in (NL-FR-ENG) and the e-mail address to which you would like us to send the verification report.
- Applications are handled according to the FIFO method. Please allow for an average waiting time of two to three weeks.
- The results of our verification apply solely to the barcode sample delivered to us.
- Our organisation is unable to perform a systematic check of all packaging of a company. You can purchase a verification device for this yourself. Consult our solution provider finder for this.
- For medicines and hazardous substances, we request that you only send the packaging (without content) or the label. If you nevertheless wish to send a physical sample with content, we ask that you display the legally required ‘EU-GHS pictograms or other warning pictograms on the outer packaging (the postal package).
To which address can you send your samples?
Tips for a readable barcode
Prevention is the best cure! Find out which common mistakes can make a barcode unreadable and how to avoid them.